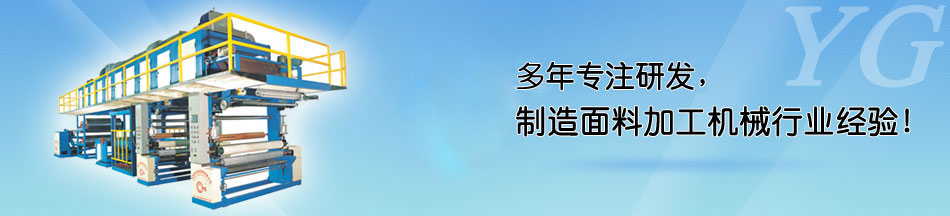
基于ISO 22304:2024《反應型膠黏劑固化控制標準》及車企實測數據
一、復合機溫度控制對固化速率的決定性作用
1. 熔膠溫度與流動性
最佳區間:110-130℃(依膠型號差異±5℃),溫度過低導致粘度激增(如120℃時粘度5000mPa·s,100℃時達15000mPa·s),影響涂布均勻性。
設備技術:采用高精度設備,實現±0.5℃超精密控溫,避免局部過熱碳化。
2. 基材預熱溫度
硬質材料(ABS/PC塑料):預熱至60-80℃(Tg溫度以下),提升膠層浸潤性,降低界面應力。
軟質材料(海綿/織物):建議40-50℃,防止高溫導致結構塌陷,實測可提升初粘強度30%(參照GB/T 2790標準)。
二、環境濕度對開放時間的非線性影響
1. 濕度與操作窗口關系
理想范圍:45-65%RH(ISO 14644-1潔凈車間標準),濕度過低(<30%RH)使開放時間延長至120秒以上,導致產線效率下降;濕度過高(>75%RH)則觸發提前固化,形成表面結皮。
動態調控方案:安裝濕度補償系統(如Despatch LAC系列),通過霧化加濕與轉輪除濕聯動,維持±3%RH波動。
2. 極端工況應對
干燥地區(如西北汽車工廠):需在涂布后增加水霧噴淋模塊(0.5-1.0g/m2水量),強制激活-NCO基團反應。
高濕環境(如華南雨季):采用氮氣幕隔離(純度99.99%),減少空氣接觸時間至5秒以內。
三、涂布厚度與壓力協同效應
1. 膠層厚度閾值
經濟性區間:0.1-0.3mm(對應涂布量25-50g/㎡),過薄(<0.05mm)導致粘接強度不足,過厚(>0.5mm)引發內應力集中,耐疲勞性下降50%(大眾VW60330測試)。
2. 復合壓力優化
硬-硬材料復合:0.6-0.8MPa高壓,消除界面微孔(孔隙率<0.1%)。
軟-硬材料復合:0.3-0.5MPa中壓配合60℃預熱,避免海綿壓縮變形超過15%(影響回彈壽命)。
四、基材表面能及預處理技術
1. 臨界表面張力要求
皮革/織物:需達38mN/m以上(達因筆測試3#液合格),低于此值需電暈處理(功率密度2.0-3.5W·min/m2)。
工程塑料(如PP/PE):必須火焰處理(甲烷流量12L/min,距離100mm),使表面能提升至44mN/m。
2. 新型預處理技術
等離子體接枝:在ABS基材上生成氨基官能團(XPS檢測N元素占比提升至8.2%),使PUR膠剝離強度提高至18N/mm(比傳統處理高40%)。
五、設備參數與工藝鏈匹配性
1. 產線速度窗口
經濟速度:8-15m/min,速度>20m/min時需啟用UV預固化(波長385nm,能量密度120mJ/cm2),否則開放時間不足導致脫膠。
2. 復合設備維護影響
膠泵精度衰減:每運行500小時后,齒輪泵間隙增大導致流量偏差>1.5%,需更換陶瓷耐磨套件。
傳熱效率下降:每月需用納米導熱膏維護加熱輥,確保傳熱系數維持在200W/(m2·K)以上。