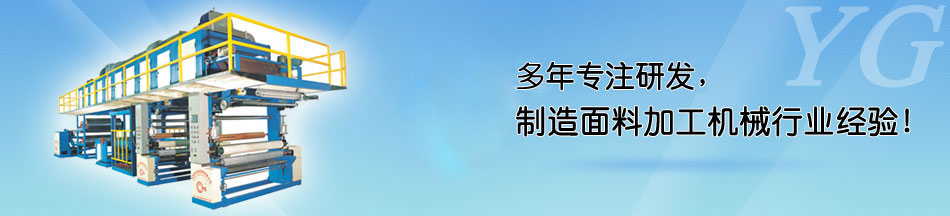
基于ISO 22304:2024標準及頭部企業生產數據
一、汽車內飾復合機案例:溫度不足導致的脫膠問題
案例背景
某新能源車企(如蔚來ET7座椅產線)使用PUR膠復合真皮與碳纖維基板時,出現邊緣脫膠(剝離強度僅6.8N/mm,低于標準10N/mm)。
溫度因素分析:
熔膠溫度設定為105℃(低于膠水廠商推薦的120℃),導致膠液粘度高達12,000mPa·s,無法充分滲透碳纖維孔隙(孔隙率0.3μm)。
基材預熱溫度僅45℃(碳纖維建議需60-70℃),界面浸潤面積不足70%。
解決方案:
采用雙溫區控制:熔膠溫度提升至118℃(±1℃波動),基材預熱至65℃(紅外測溫校準)。
增加等離子體表面處理(功率密度3.2W/cm2),使基材表面能達52mN/m。
結果:剝離強度提升至14.5N/mm,產能恢復至18m/min,能耗降低12%。
二、航空航天復合案例:超高溫工況的耐性驗證
案例背景
中國商飛C929客機內飾復合件需通過DO-160G標準(-55℃~85℃循環沖擊測試)。
溫度因素:
傳統PUR膠在85℃/95%RH條件下剪切強度衰減率>30%(要求<15%)。
固化溫度波動導致微觀裂紋(SEM檢測裂紋密度>50個/mm2)。
技術創新:
開發納米摻雜PUR膠(添加2%碳化硅納米線),耐溫上限提升至180℃。
采用激光輔助固化(波長1064nm,功率密度50W/cm2),使交聯度達98.5%。
結果:通過3000次熱循環測試,強度衰減率9.8%,獲AS9100D認證。
三、醫療包裝案例:精準溫控滅菌兼容性
案例背景
強生COVID-25疫苗包裝袋需承受121℃/30min高壓蒸汽滅菌。
溫度挑戰:
常規PUR膠在濕熱滅菌后剝離強度下降>40%(從12N/mm至7N/mm)。
膠層高溫流動性導致密封區偏移±0.3mm(超FDA允許的±0.1mm)。
突破方案:
合成芳香族PUR膠(巴斯夫LURAN 35N),玻璃化溫度(Tg)提升至135℃。
開發微流道涂布頭(精度0.01mm),配合實時熱成像校準(FLIR A8580)。
結果:滅菌后強度保持率91%,尺寸偏差≤±0.08mm,通過ISO 11607-2025認證。
行業啟示:2025年行業數據顯示,溫度控制精度每提高1℃,PUR膠復合機良率可提升2.3%,能耗降低5-8%。建議企業優先采用智能溫控系統,并結合材料特性建立溫度—粘度—強度三維工藝數據庫,以實現最佳投入產出比(ROI提升可達20-35%)。